Zwischen BYD und Bürokratie
Transformation statt Tradition: Die Wettbewerbssituation der deutschen Autoindustrie verschlechtert sich weiter. Im globalen Wettbewerb steht sie gegenüber der erstarkenden Konkurrenz etwa aus China zunehmend unter massivem Kosten- und Innovationsdruck. Und zwar gleichzeitig. Durch Digitalisierung, Robotik und strategische Partnerschaften will sie ebenso wie mit plattformbasierten Architekturen, Lean Management und smarteren Lieferketten ihre technologische Führung zurückgewinnen und ökonomisch effizienter werden. Und doch belegt die Wettbewerbsstudie von Alvarez & Marsal, dass sich viele Unternehmen wegen der Überregulierung hierzulande, hohen Energie- und Lohnkosten gezwungen sehen ins Ausland zu verlagern. Das gilt nach der Produktion nun auch für Forschung und Entwicklung..
Die Disruption konfrontiert Deutschlands Autobauer mit fundamentalen Herausforderungen. Sie müssen Elektrifizierung und Digitalisierung, Dekarbonisierung und neue Mobilitätskonzepte umsetzen. Und zwar schnell und kosteneffizient. Innovationen voranzutreiben und dabei gleichzeitig Ausgaben zu senken, um im globalen Wettbewerb zu bestehen – das klingt nach einem unauflösbaren Konflikt. Aber die deutsche Autoindustrie ist entschlossen, ihre Zukunftsfähigkeit zu beweisen.
Das zeigt unsere aktuelle Wettbewerbsstudie zur deutschen Industrie von Alvarez & Marsal. Demnach beurteilen 24 Prozent der Unternehmen aus der Automobilbranche ihre Wettbewerbssituation als schwierig bis sehr schwierig. Damit ist sie der skeptischste Industriesektor in der gesamten Befragung. Allerdings: Statt zu lamentieren, investieren die Unternehmen in Innovationsfähigkeit – 41% haben bereits jetzt ihre Budgets dafür erhöht, weitere 21% planen es für dieses Jahr und erwarten davon signifikante Effekte. Dass die Firmen trotz der angespannten wirtschaftlichen Lage in Ideen investieren, ist ein gutes Zeichen. Sie wollen technologische Führung und Deutungshoheit zurückgewinnen. Dafür müssen sie Investitionsmöglichkeiten gezielt priorisieren und ihre Effekte kontinuierlich messen, um einen maximalen Return on Investment zu sichern.
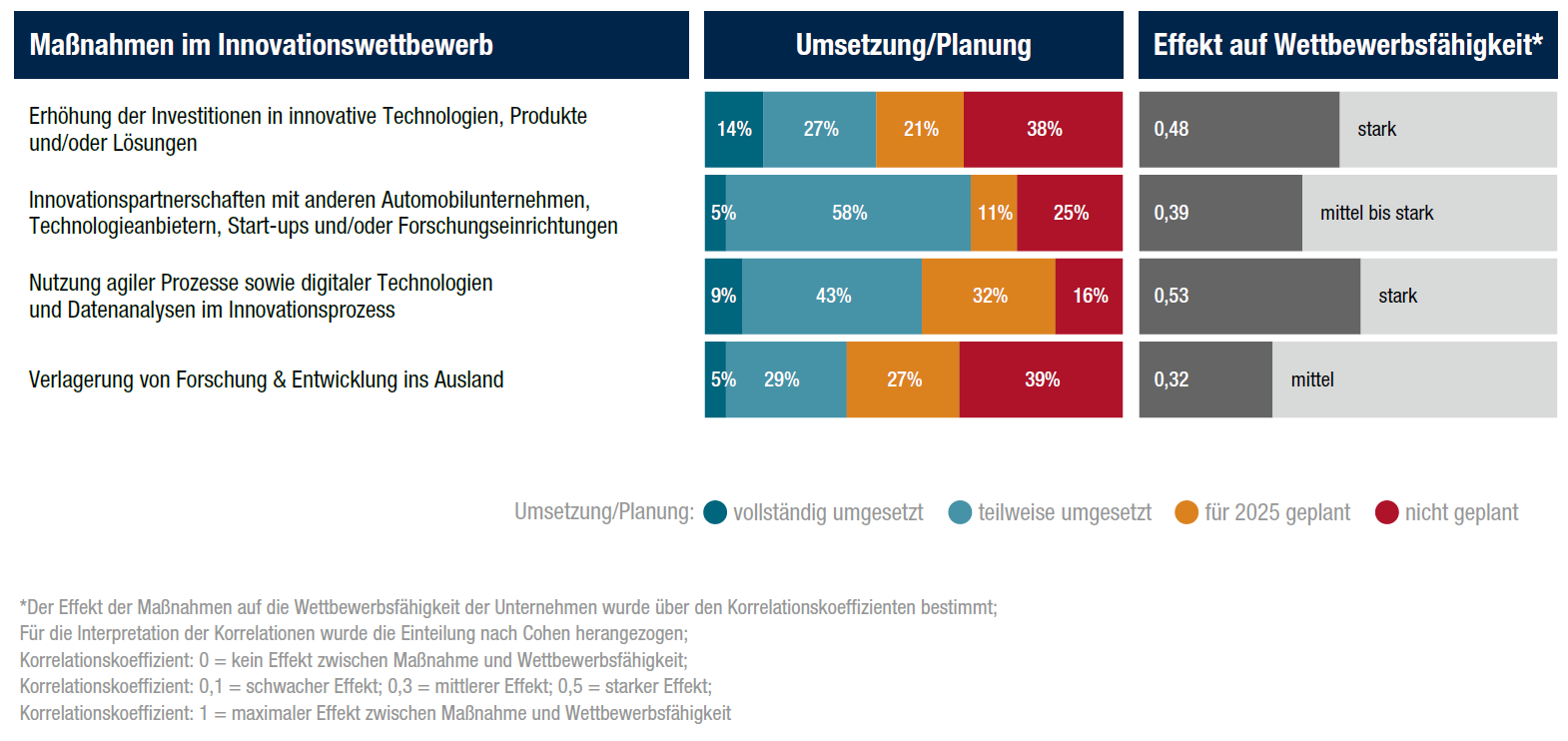
Der Wandel zur E-Mobilität zwingt die Autoindustrie, sich neu zu erfinden und den traditionellen deutschen Erfindergeist auf Zukunftsthemen auszurichten. Etwa: Reichweite maximieren, Ladezeit minimieren und ein Second Life für Akkus sichern. Automatisiertes Fahren ermöglichen. Das Kundenerlebnis durch Over-the-Air-Updates für neue Funktionen steigern. Darum geht es. Und um die Frage: Schaffen autonome Fahrzeuge neue Geschäftsmodelle und eine effiziente Integration in multimodale Verkehrssysteme?
Es sind die großen technologischen Fragen, die der Automobilesektor nicht zuletzt auch kulturell beantworten muss. Zum Beispiel durch Innovationspartnerschaften. Sie treiben komplexe technologische Entwicklungen oft erfolgreicher voran, erreichen früher die Marktreife und helfen, Risiken auf die Partner zu verteilen. Solche Kooperationen haben allerdings erst 5% der Unternehmen vollständig und weitere 58% zumindest teilweise realisiert. Die Automobilindustrie ist gerade dort auf Partnerschaften angewiesen, wo sie den Technologieanschluss verpasst hat – beispielswiese im Bereich Batterietechnologie. Und auch, was agile Entwicklungsprozesse, digitale Technologien und Datenanalysen betrifft, wollen die Unternehmen aufholen: 9% von ihnen haben sie komplett eingeführt; immerhin 75% arbeiten an deren Umsetzung oder planen dies, um künftig kreativer und effizienter agieren oder verändertes Kundenverhalten besser voraussagen zu können.
Zur Wahrheit gehört auch, dass viele Unternehmen (34%) nicht nur die Produktion, sondern auch Forschung und Entwicklung ins Ausland verlagern. Das hängt mit der Verfügbarkeit von Fachkräften und Lohnkosten zusammen, mit kultureller Nähe zu Zielmärkten und einer geringeren Regulierung. Auch deshalb planen weitere 27% der Firmen diesen Schritt. Hierzulande leiden sie nicht nur unter den Energiekosten (76%) und der konjunkturellen Entwicklung (72%), sondern vor allem unter der Bürokratie. 80% der Befragten sehen in Regulierung den größten Standortnachteil in Deutschland, was man durchaus als Entfremdung der Wirtschaft von der Politik interpretieren könnte. Zusätzlich fühlen sich 70% der Unternehmen durch veränderte Handelsbeziehungen wie Zölle belastet. Auch deshalb kommen viele an einer Standortverlagerung nicht vorbei. Sie dient zugleich dem Kostenmanagement.
Der globale Wettbewerb, in dem Länder wie China nicht nur technologisch in Führung gehen, setzt die deutsche Autoindustrie massiv unter Kostendruck. Die Transformation ist mit hohen Investitionen verbunden. Wenn Unternehmen zwei Plattformen parallel betreiben – eine für Verbrenner, eine für E-Autos – erfordert das enorme Ressourcen. Die Hersteller müssen sich mehr denn je anstrengen, übergreifende Effizienzsteigerung zu erzielen.
Die Maßnahmen gehen sie konsequent an. 25% der Hersteller haben bereits plattformbasierte Architekturen eingeführt, also modulare Baukästen, die Modelle effizienter skalieren lassen. Weitere 39% sind in der Umsetzung. Ein Drittel der Unternehmen setzt auf strategisches Lieferantenmanagement mit klaren Konditionen – fast die Hälfte ist dabei, das ebenfalls einzuführen. Es geht ums Ganze – und zwar entlang der gesamten Wertschöpfungskette.
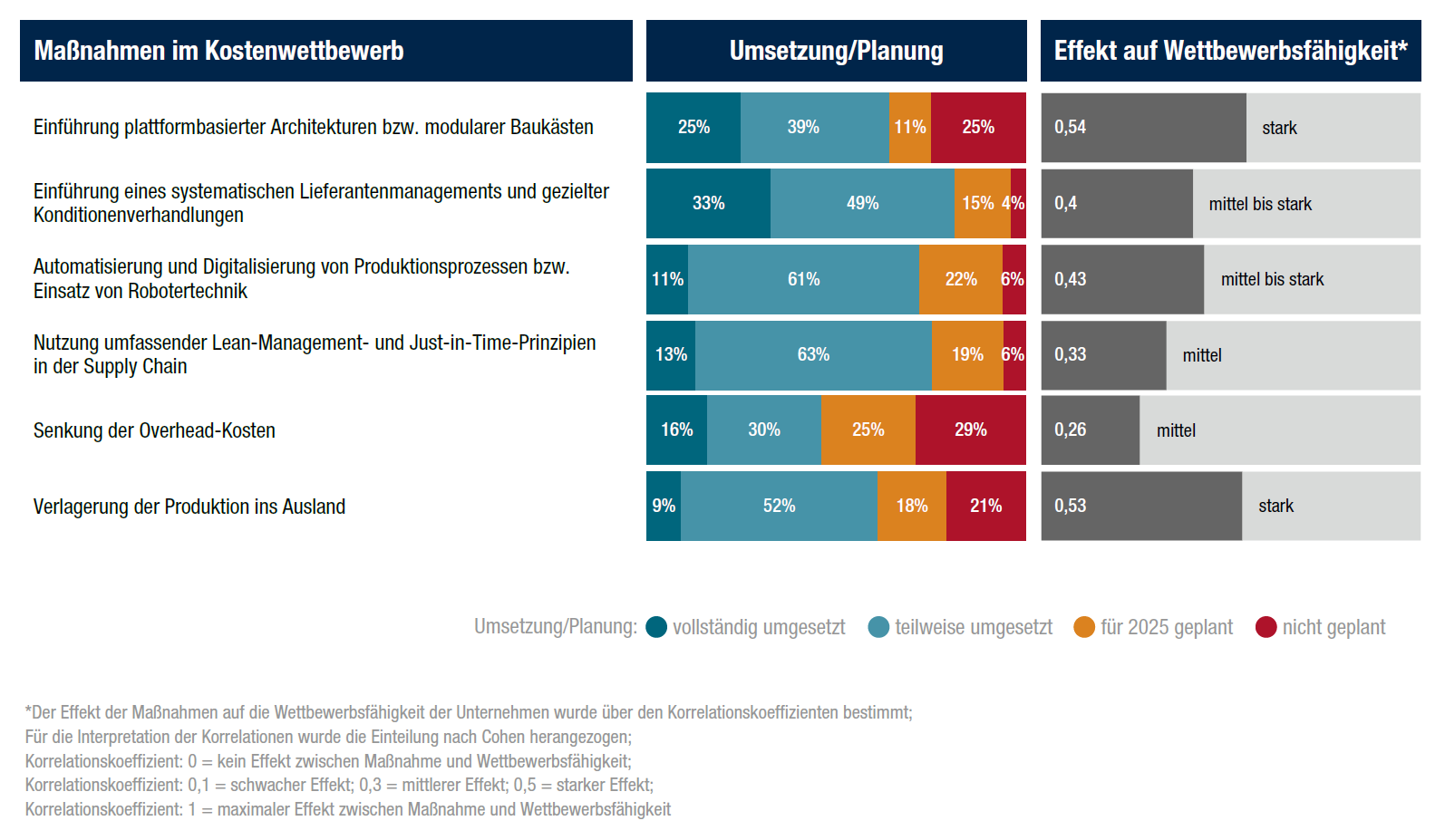
Gleichwohl ruckelt es noch bei der Produktion: Nur 11% der Unternehmen haben ihre Prozesse bereits vollständig automatisiert. Aber 61% arbeiten daran. Das gleiche Bild bei Lean Management und Just-in-Time: Gerade einmal 13% nutzen diese Prinzipien umfassend – 63% holen auf. Es geht nicht nur um Effizienz. Es geht um Beweglichkeit. Um Resilienz in einem System, das sich nicht mehr auf verlässliche Lieferzeiten und stabile Margen verlassen kann.
Und weil auch die Geografie inzwischen zur Kostenfrage geworden ist, haben 61% ihre Produktion bereits ins Ausland verlagert – meist dorthin, wo Löhne, Energie und Bürokratie weniger fordernd sind. Weitere 18% planen diesen Schritt für 2025. Steuerlich vorteilhaft, geopolitisch kalkulierbarer – und betriebswirtschaftlich fast schon zwingend.
Grundsätzlich wirken derzeit zwei Hebel auf die Wettbewerbsfähigkeit – die modulare Plattformstrategie und die Verlagerung der Produktion. Lieferantenmanagement und Produktionsautomatisierung folgen dicht dahinter. Noch viel zu häufig sind Overhead-Kosten stille Ergebnisfresser. Die Möglichkeiten der Senkung werden oft unterschätzt. Sie müssen aber konsequent genutzt werden, um krisenresilient zu sein und Ressourcen für Innovation und Wachstum freizumachen.
Gerade vor dem Hintergrund der volatilen globalen politischen Lage ist eine gesteigerte Wettbewerbsfähigkeit heute wichtiger denn je – zugleich aber schwerer zu erreichen. Allein die Unsicherheiten rund um globale Handelszölle führen zu komplexeren Lieferketten und zwingen Lieferanten und Kunden zu intensiveren Verhandlungen, um die Last gemeinsam zu schultern. Um die Folgen der Disruption erfolgreich zu bewältigen, müssen einzelne Akteure ihre Partikularinteressen zurückzustellen.
Die gesamte Studie erhalten Sie hier: